Formability of steel plates for the automotive industry
The Department of Manufacturing Technology FME CTU in Prague cooperates with ŠKODA AUTO a.s. in the areas of forming. Mutual research on the formability of deep-drawn steel sheets used for the production of car body parts. The work was focused on describing the effect of the strain rate on the position of the forming limit curve (FLC). A methodology for evaluating the effect of the deformation rate on the position of the forming limit curve (FLC) was created for use in numerical simulations.
The research was carried out for selected materials commonly used for car body construction. The properties were evaluated by tensile testing and other technological tests at appropriate loading rates (Nakajima). The evaluation of the test results was carried out using the ARGUS and ARAMIS measuring systems. The obtained results were also monitored using numerical simulations.
The motivation for the research was to find the effect of the deformation rate on the stability of the pressing process, which will lead to financial savings. These savings are also given by increasing the stability of the pressing process.
As part of the research, it was necessary to solve a number of sub-tasks. One of them was the adhesion of deformation networks to the surface of the sheet metal. The cohesion of the network is key to the readability of the network during deformation. The cohesion of the network depends on the degreasing of the surface, the type of varnishes and compliance with the technological process of their application.
The experiments show that with increasing strain rate, the plastic properties of the material decrease (ductility decreases) and the strength properties increase (yield strength and tensile strength, but their ratio deteriorates).
From a relatively wide range of measurements performed, various variants of FLC curves were created: optimistic, pessimistic, average for speeds of 2 mm/s and 17 mm/s, average of all measured values.
As part of the cooperation with ŠKODA AUTO, a dissertation was created (Ing. Vít Novák, Ph.D.), which establishes the methodology for testing automotive sheet metal, the methodology for compiling a material card, and verifies the measured data using numerical simulation. To create the material card, an approximation of the true stress – true stress dependence was performed for various strain rates.
Different tool geometries were used for verification. One of the main tools for verification of the results was the Cross die punch. A created material card was used to describe the material behaviour.
The deformation values achieved by the ARGUS and ARAMIS methods were compared with numerical simulation.
System | Stroke [mm] | Stroke speed [mm/s] | Thinning [%] |
ARGUS | 20 | 17 | 25 |
ARAMIS | 20 | 17 | 27 |
Autoform | 20 | 17 | 27,1 |
Furthermore, the risk of failure for speeds of 2 and 17 mm/s was compared in a numerical simulation. It was shown that the material formed at higher speeds has a higher risk of failure.
In collaboration with:
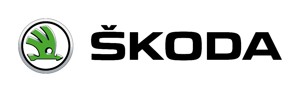
Contact:
Ing. Vít Novák, Ph.D.
Department of Manufacturing Technology FME CTU in Prague
E-mail: vit.novak@fs.cvut.cz